Understanding Pressure Die Casting Tools for Optimal Metal Fabrication
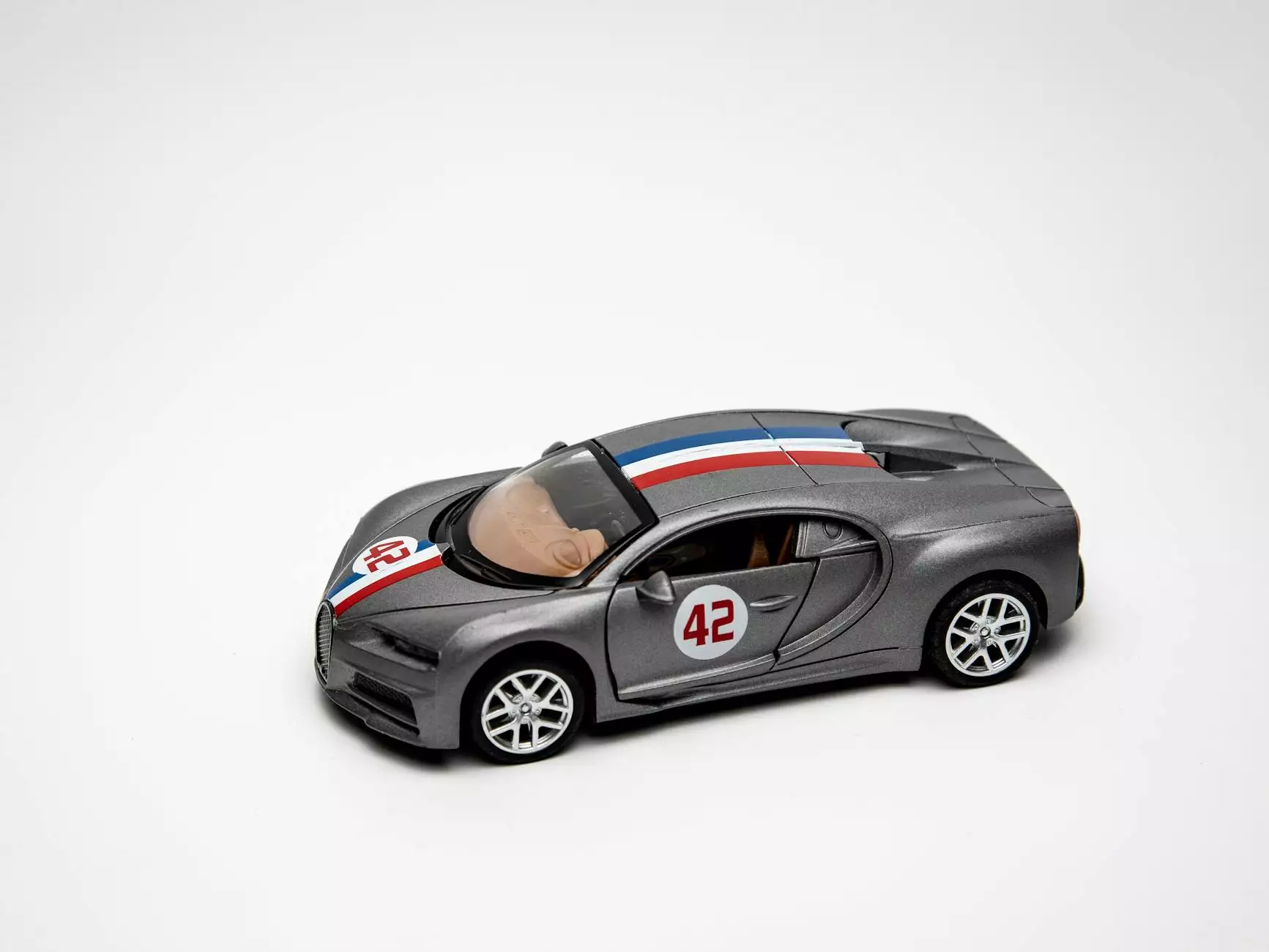
In the world of metal fabrication, precision and efficiency are paramount. One of the key processes that ensure these attributes in manufacturing is pressure die casting. This method allows for the production of complex shapes with high dimensional accuracy, making it essential for various industries including automotive, aerospace, and electronics.
What is Pressure Die Casting?
Pressure die casting is a manufacturing process where molten metal is injected into a mold at high pressure. This technique is revered for its ability to create intricate designs and robust parts with minimal defects. The process not only enhances the productivity of metal components but also significantly reduces waste compared to other casting methods.
How Does Pressure Die Casting Work?
The pressure die casting process involves several key steps:
- Preparation of the Mold: A two-part mold, typically made from steel or iron, is designed based on the specifications of the desired component.
- Melting the Metal: Metal alloys, most commonly aluminum and zinc, are melted in a furnace to reach a liquid state.
- Injection of Molten Metal: Using a high-pressure injection system, the molten metal is forced into the mold cavity.
- Cooling and Solidification: The metal cools and solidifies rapidly, forming a solid part within the mold.
- Mold Extraction: Once cooled, the mold is opened, and the casting is ejected.
The Importance of Pressure Die Casting Tools
To achieve the best results in pressure die casting, the right tools are essential. These tools not only determine the quality of the finished product but also influence the overall efficiency of the metal fabrication process. Let's delve into the different types of tools involved in pressure die casting:
1. Die Casting Machines
Die casting machines are at the heart of the pressure die casting process. These machines come in various configurations, including:
- Hot Chamber Machines: Ideal for metals with low melting points, these machines continuously feed molten metal into the system.
- Cold Chamber Machines: Suitable for metals with higher melting points, these machines require manual insertion of the metal before each injection.
2. Mold Components
The mold itself consists of several components that ensure the accuracy and quality of the castings:
- Cavity Plates: The parts that form the shape of the casting.
- Core Inserts: Used to create internal features of the casting.
- Cooling Channels: Integrated within the mold to reduce cooling time and maintain dimensional stability.
3. Injection Mechanisms
The injection system is crucial for controlling the flow and pressure of the molten metal as it fills the mold. Technologies include:
- Piston Injection: Provides consistent and high-pressure injection of metal.
- Plunger Injection: Uses a plunger mechanism for less viscous metals.
Choosing the Right Pressure Die Casting Tools
Selecting the appropriate tools for pressure die casting is critical for optimizing performance. Here are the factors to consider:
1. Material Compatibility
Ensure that the tools you select are compatible with the materials you plan to work with. Consider using molds made from high-quality steel or tungsten alloys, as they offer better durability and heat resistance.
2. Precision and Accuracy
Look for tools that provide the necessary precision for your specific applications. Advanced CNC machining can significantly enhance the accuracy of molds.
3. Production Volume
The intended production volume will also influence your choice. For high-volume production, investing in automated die casting machines may save time and reduce labor costs.
Benefits of Pressure Die Casting Tools
Implementing the right pressure die casting tools can yield numerous benefits for businesses:
1. Cost Efficiency
By minimizing scrap rates and optimizing material usage, businesses can achieve substantial cost savings. Additionally, the rapid production capabilities of pressure die casting can enhance turnaround times, further improving profitability.
2. High Production Rate
Pressure die casting allows for the quick production of large quantities of parts without compromising quality, making it ideal for industries with high demand.
3. Enhanced Product Quality
Thanks to the precise nature of pressure die casting, the final products exhibit excellent surface finishes and dimensional tolerances, often eliminating the need for extensive post-processing.
Applications of Pressure Die Casting
The applications for pressure die casting are vast and varied. Here are a few notable uses:
1. Automotive Industry
Pressure die casting is widely used in the automotive sector for producing components such as:
- Engine blocks
- Transmission housings
- Suspension components
2. Aerospace Industry
In aerospace, precision and weight reduction are critical. Pressure die casting helps manufacture lightweight structures that meet stringent regulatory standards.
3. Electronics Industry
For electronics, housing, and component parts are produced with great accuracy, ensuring reliable functionality and enhanced performance.
Future Trends in Pressure Die Casting
The future of pressure die casting tools looks promising, with ongoing innovations driving efficiency and quality. Key trends include:
1. Adoption of Industry 4.0 Technologies
Integrating smart technology such as IoT and AI into die casting operations can lead to improved predictive maintenance, reduced downtime, and enhanced quality control.
2. Sustainable Practices
As environmental concerns continue to rise, many manufacturers are focusing on sustainability by optimizing energy consumption and recycling materials.
3. Advanced Materials
The exploration of new alloys and composite materials can offer even better performance in high-stress applications, expanding the scope of pressure die casting.
Conclusion
In conclusion, investing in high-quality pressure die casting tools is essential for any business in the metal fabrication sector. By understanding the processes, selecting the right tools, and keeping abreast of industry trends, manufacturers can significantly enhance their production capabilities and product quality. The future holds great potential for businesses that embrace the advancements in pressure die casting technology, making it a vital consideration for those looking to maintain a competitive edge in the marketplace.
For more information on premium metal fabricators and pressure die casting tools, visit DeepMould.net.