Unlocking Potential: The Role of Die Casting in the Automotive Industry
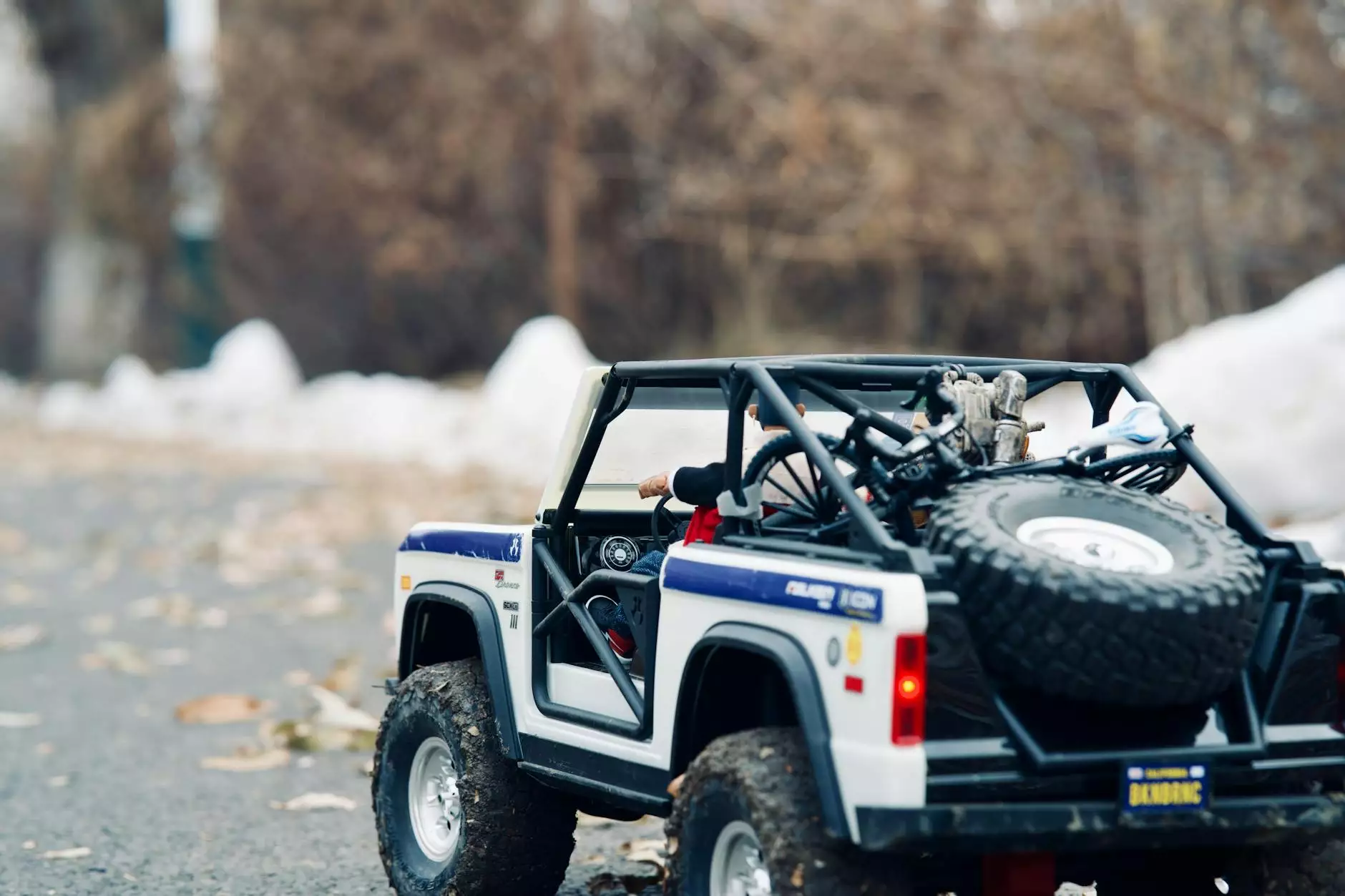
In the world of automotive manufacturing, precision, durability, and weight savings are vitally important. Among various manufacturing processes, die casting has emerged as a leading method for producing intricate components with exceptional quality. This process is especially prevalent within the realm of metal fabricators, including companies like DeepMould.net, which specialize in creating high-quality automobile parts through advanced techniques.
The Fundamentals of Die Casting
Die casting is a metal casting process characterized by forcing molten metal under high pressure into a mold cavity. The molds, known as dies, are crafted meticulously to ensure precision and quality. This manufacturing technique can work with a variety of metals, but it is most commonly used with aluminum, zinc, and magnesium—elements that are ideal for the automotive industry's needs due to their lightweight and strong properties.
The Process of Die Casting
The die casting process generally involves several key steps:
- Preparation of the Die: The die is prepared, cleaned, and lubricated to ensure smooth metal flow and easy component removal.
- Melting the Metal: Metal is melted in a furnace and brought to a temperature that allows it to flow easily.
- Injection: The molten metal is injected into the die at high pressure. This step is crucial for the detailed and complex shapes typical in automotive parts.
- Curing: The metal solidifies within the die, forming the desired shape.
- Removing the Casting: Once solidified, the die is opened, and the casting is ejected.
Key Advantages of Die Casting in Automotive Manufacturing
The benefits of using die casting in the automotive industry are numerous:
- High Dimensional Accuracy: Parts produced through die casting have excellent dimensional consistency which leads to a decrease in assembly time and costs.
- Complex Geometries: The process allows for intricate shapes and designs, which is essential for modern automotive components.
- Cost-Effective Production: While the initial setup costs can be high, the long-term benefits include lower production costs per unit, particularly for large quantities.
- Durability and Strength: Components made through die casting typically exhibit remarkable strength, making them reliable in high-performance applications.
- Weight Reduction:Die casting allows manufacturers to create lighter parts without compromising on strength, aiding in fuel efficiency.
Applications of Die Casting in the Automotive Sector
In the automotive industry, die casting finds its applications in various components:
- Engine Components: Such as oil pans, cylinder heads, and valve covers.
- Transmission Housings: Offering strength while keeping weight low.
- Structural Components: Including brackets and support structures that benefit from precision fitting.
- Chassis Parts: Ensuring robust performance and durability.
- Cosmetic Elements: Enhancing the aesthetic appeal of vehicles, such as trim pieces.
The Future of Die Casting in Automotive Manufacturing
As the automotive industry evolves, so does the role of die casting. With the advent of electric vehicles (EVs) and a push towards more sustainable practices, die casting remains relevant as manufacturers seek efficient and environmentally friendly solutions. Innovations such as improved die materials and enhanced production techniques are further paving the way for high-volume production of parts that meet rigorous industry standards.
Embracing Sustainability in Die Casting
With a growing emphasis on sustainability, the die casting automotive sector is adapting. The use of recycled metals and energy-efficient processes can significantly reduce the carbon footprint associated with manufacturing. As forward-thinking companies like DeepMould.net implement eco-friendly practices, the automotive industry continues to transform, aligning with global sustainability goals.
Technological Advancements Impacting Die Casting
Recent advancements in technology also play a pivotal role in enhancing die casting outcomes:
- 3D Printing: Used for rapid prototyping, allowing for quicker innovation and design iterations.
- Simulation Software: Predicts the behavior of molten metal in dies to optimize designs and minimize defects.
- Automated Processes: Robotics are playing a vital role in increasing production rates and maintaining quality.
Choosing the Right Partner for Die Casting Automotive Needs
When it comes to selecting a provider for die casting automotive components, considerations should include:
- Industry Experience: A proven track record in die casting within the automotive market.
- Technology Utilization: The adoption of the latest technologies to enhance quality and efficiency.
- Quality Assurance: Rigorous testing and compliance with industry standards.
- Customer Support: A responsive and knowledgeable support team ready to assist with any concerns.
Conclusion: The Undeniable Value of Die Casting in Automotive Industry
As the automotive landscape continues to change, die casting remains a cornerstone of production efficiency and quality. The process not only meets the demanding requirements of modern vehicles but also adapts to the evolving needs towards sustainability and innovative manufacturing practices. Companies like DeepMould.net, with their commitment to excellence and innovation in the die casting automotive field, are poised to lead the charge into a productive future. Whether it’s through increasing vehicle performance or enhancing aesthetic appeal, the role of die casting is crucial and will undeniably shape the automotive industry for years to come.