Injection Molding in the Automotive Industry: Revolutionizing Manufacturing
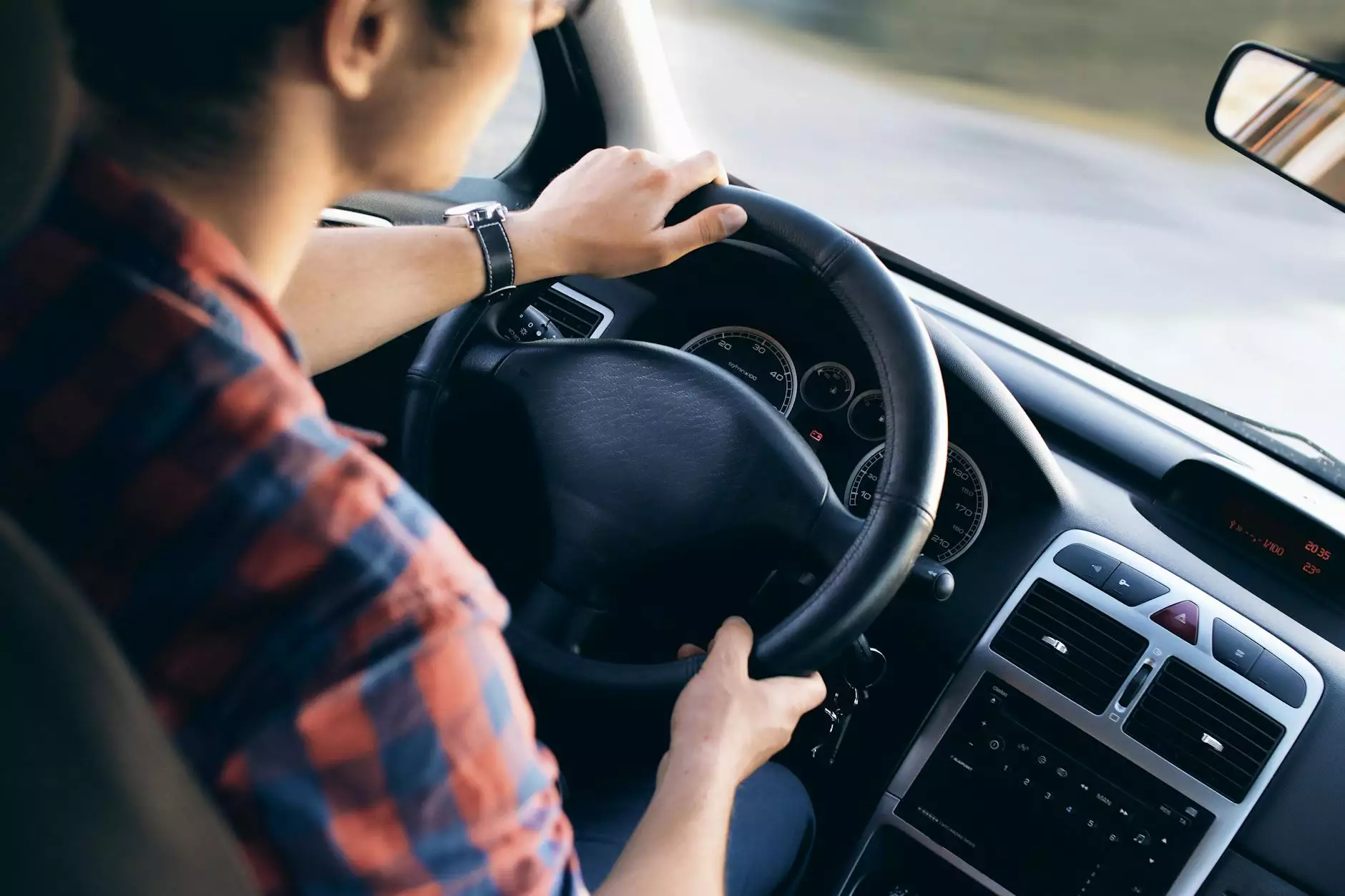
In the competitive landscape of modern manufacturing, injection molding automotive components have emerged as a pivotal technology. This process has not only transformed the way vehicles are produced but has also enhanced the efficiency and quality of automotive parts. As the automotive industry continues to evolve, understanding the nuances of injection molding is essential for manufacturers aiming for higher productivity and cost-effectiveness.
Understanding Injection Molding
Injection molding is a manufacturing process whereby raw plastic materials are melted and injected into molds. Once cooled, the molds are removed, resulting in a solidified part that can be used for various applications. This method is particularly advantageous in producing intricate shapes and complex geometries, making it ideal for the automotive sector.
Key Advantages of Injection Molding in Automotive Manufacturing
Adopting injection molding within the automotive industry provides numerous benefits, including:
- High Efficiency: The injection molding process allows for rapid production of parts. High production rates enable manufacturers to meet the growing demand for vehicles without compromising quality.
- Cost-Effective: Once the mold is created, the cost per part decreases significantly, making injection molding a cost-effective solution in large production runs.
- Design Flexibility: Injection molding supports complex designs and intricate details, enabling engineers to innovate and improve the functionality of automotive components.
- Material Variety: A wide range of materials can be used in the injection molding process, including thermoplastics and thermosets, providing flexibility in component properties.
- Reduced Waste: The injection molding process minimizes material waste, which is not only cost-effective but also environmentally friendly.
Injection Molding Process in the Automotive Sector
The injection molding process consists of several key stages:
1. Material Selection
The first step involves selecting the appropriate materials that can withstand automotive performance standards. Common materials used include:
- ABS (Acrylonitrile Butadiene Styrene): Known for its toughness and impact resistance.
- Polypropylene: Valued for its lightweight and chemical resistance properties.
- PVC (Polyvinyl Chloride): Used for electrical insulation components due to its strong electrical resistance.
2. Mold Design
Creating an effective mold is crucial for successful injection molding. This stage involves:
- Mold Type Selection: Choosing between single or multi-cavity molds based on production needs.
- Cooling System Design: Designing an efficient cooling system to expedite production times and ensure uniformity in part dimensions.
3. Injection Phase
During this phase, the selected plastic materials are heated until they reach a molten state and are then injected into the mold under high pressure. This process is vital for achieving detailed designs and maintaining material integrity.
4. Cooling and Ejection
After the injection phase, the molten material must cool and solidify. Once cooled, the mold opens to eject the finished part. This stage is crucial in maintaining the dimensional accuracy and surface finish of automotive components.
Recent Innovations in Injection Molding for Automotive Applications
The automotive industry is constantly evolving, and injection molding technology is no exception. Recent innovations include:
1. Advanced Materials
With the push for lighter vehicles and better performance, manufacturers are exploring advanced composite materials that enhance strength while reducing weight.
2. 3D Printing Integration
The integration of 3D printing with injection molding allows for rapid prototyping, enabling quicker adjustments and validations of design before full-scale production.
3. Sustainable Practices
There is a growing emphasis on sustainability in automotive manufacturing. Many companies are adopting biodegradable materials and recycling programs to reduce their carbon footprint. These practices align well with modern consumers’ eco-conscious preferences.
Challenges in Injection Molding for the Automotive Industry
While the benefits of injection molding are substantial, there are challenges that manufacturers must address, including:
1. High Initial Costs
The upfront investment in mold creation and machinery can be significant. However, this cost can be recovered through high-volume production savings over time.
2. Quality Control
Maintaining consistent quality across production runs is essential. Implementing rigorous quality control measures and utilizing modern inspection technologies can help address this challenge.
3. Skilled Labor Shortages
The injection molding process requires skilled operators and technicians. Developing training programs and retaining talent are crucial for maintaining operational efficiency.
Future Trends in Injection Molding and the Automotive Industry
As technology advances, several trends are shaping the future of injection molding in the automotive sector:
- Smart Manufacturing: The integration of IoT (Internet of Things) will lead to smarter production lines with real-time monitoring and analytics.
- Automation: Automation in the injection molding process enhances speed, reduces human error, and increases overall efficiency.
- Customization: For automotive manufacturers, the ability to customize parts quickly through injection molding is becoming increasingly important to meet diverse consumer needs.
Conclusion: Embracing Injection Molding in the Automotive Industry
In conclusion, the role of injection molding in the automotive industry is more critical than ever. By leveraging the advantages of this manufacturing technique, automotive companies can enhance their production processes, reduce costs, and offer innovative products that meet consumer demands. As the automotive landscape continues to evolve, staying abreast of advancements in injection molding technology will be essential for maintaining a competitive edge.
For more information on using injection molding automotive solutions, visit Deep Mould and discover how we can assist you in transforming your manufacturing processes effectively.