The Benefits of Industrial Laser Welders for Metal Fabricators
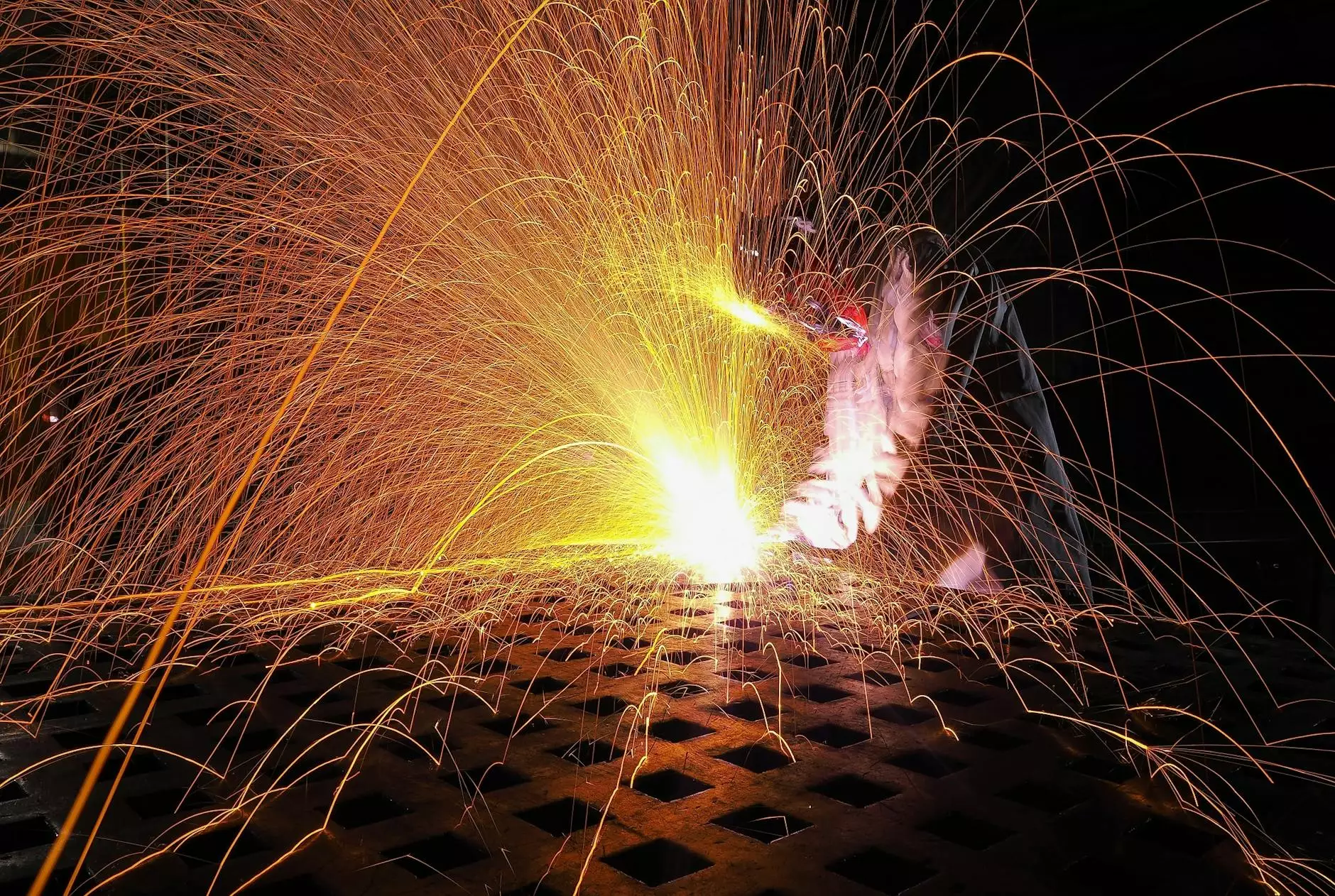
Introduction
When it comes to metal fabrication, staying ahead of the competition is crucial. In today's fast-paced business environment, efficiency, accuracy, and quality are the key factors that determine success. As a metal fabricator, investing in advanced technologies can significantly enhance your manufacturing capabilities. One such technology that has revolutionized the industry is the industrial laser welder.
What are Industrial Laser Welders?
Industrial laser welders are cutting-edge devices used in metal fabrication processes to create precise and strong welds. Unlike traditional welding techniques, laser welders utilize focused laser beams to melt and join metal components together. This technology offers an array of advantages for metal fabricators, making it a sought-after choice.
Enhanced Precision and Quality
One of the primary benefits of industrial laser welders is their exceptional precision. The laser beams produced by these devices are highly focused, allowing for precise control over the welding process. This ensures accurate alignment and minimizes the risk of errors or imperfections in the welds. As a result, the overall quality of the fabricated metal products is significantly improved.
Increased Efficiency and Productivity
With industrial laser welders, metal fabricators can experience a substantial boost in efficiency and productivity. The speed at which laser welders can create weld joints is remarkable, significantly reducing the overall production time. Additionally, their automated features and advanced programming capabilities streamline the workflow, minimizing the need for manual intervention. This not only saves time but also reduces labor costs and enhances overall operational efficiency.
Wide Range of Applications
Industrial laser welders are incredibly versatile and can be used in various metal fabrication applications. Whether you're working with stainless steel, aluminum, or other alloys, laser welders can effectively join different metals together with precision. From intricate details on small components to large-scale welding projects, the flexibility of laser welders makes them an invaluable tool for metal fabricators.
Cost-Effective Solution
While the initial investment in industrial laser welders may seem significant, they offer substantial long-term cost savings. Laser welders reduce material waste by minimizing heat-affected zones during the welding process. This leads to less material distortion, resulting in higher yields and reduced scrap. Additionally, the efficiency and productivity gains mentioned earlier translate to increased output without compromising quality, ultimately boosting your bottom line.
Improved Safety
Compared to traditional welding techniques, industrial laser welders provide a safer working environment for your employees. They minimize the risk of accidents and injuries associated with open flames, sparks, and harmful fumes. Laser welding is a non-contact process, eliminating the need for physical contact with the weld material. This greatly reduces the risk of burns and other related hazards.
The Future of Metal Fabrication
As technology continues to advance, industrial laser welders will undoubtedly play a vital role in the future of metal fabrication. Their incredible precision, efficiency, and versatility make them an indispensable tool in the industry. By investing in these cutting-edge devices, metal fabricators can stay at the forefront of innovation and gain a competitive edge in the market.
Conclusion
DPLaser understands the demands and challenges faced by metal fabricators in today's business landscape. Our cutting-edge industrial laser welders are designed to meet and exceed your expectations, delivering exceptional weld quality, increased productivity, and cost savings. Experience the future of metal fabrication with DPLaser's industrial laser welders and elevate your manufacturing capabilities to new heights.